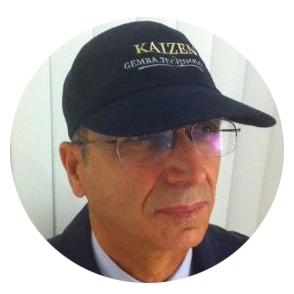
Mr Farhad Azimi
According to the expert studies, success rates of traditional Improvement activities are only 5 to 10%. I am a Lean-TPS coach with 20 years of experience, having coached more than 100 companies in diverse manufacturing industries and the service sector. I noticed Lean activities might sustain in only a few organizations that practice”Kaizen Management Style” through their hierarchy, from top managers down to the lowest level.
I have a Japanese Senior Lean Consultant partner, Dr. Kawada Ph.D. in Economics with 35 years practical experience in Industry and more than a decade research and teaching experience. At Meijo Univ. in Nagoya, Japan. He has invented a pretty powerful system, which is integrating Lean-TPS and Lean Accounting.
When Dr. Kawada’s system is used, success rates leap up to 90% or more. The reason behind it is the linkage between continuous Kaizen Activities and a financial dashboard which consist of NCTR (Net Conversion Time Ratio), BSQ (Balance Sheet Quality), PP (Profit Potential), and SCCC (Supply Chain Conversion Cycle) which are to support of “Productivity”,”Business Sustainability”, “Profitability”, and”Cash Flow” respectively. The dashboard becomes shared under a close watch by all department heads at all times. This is the main reason to hold all department managers accountable and encourage them to resolve their business problems by themselves or induce their subordinates to think and do changes for the better, or Kaizen. Managers’ “Commitment and Support”, the two vital elements to sustain Lean Activities can be generated by this system.
Objective:
Experienced LEAN-Toyota Production System coach, Shop Floor Manager, Kaizen and Lean Manufacturing specialist, have a great passion to execute, consult and learn constantly. Communicate well, dig deep to find out employee’s needs and preferences and link them with the company ‘s goal and objectives. Create a winning culture. Encourage all employee participation and eliminate wastes to improve quality productivity and profitability.
Skills Expertise and Accomplishments:
• Designed, executed and coached lean initiatives such as; Shop Floor Management, Policy Deployment, Quick Response Quality Control, Employee and Customer satisfaction, Reward and Award System, Value Stream Mapping, Cost Management, Value Engineering and Value Analysis, Just In Time Production, Cell Design Operation, Waste Elimination, Single Minute Exchange of Dies, Low Cost Automation, Total Productive Maintenance, Visual Control System, 5S, DMAIC, A3, Visual Management, Kaizen Board and Project Board, Multi Skill Workers Training, Balanced Scorecard, and Supply Chain Management.
• Planned and Organized 5 Day kaizen workshops to address company and divisional issues using appropriate shop floor initiatives in over 120 companies in diverse industries. Most of the companies could improve business metrics from 10 to 20%, annually. In one case the company made improvements up to 100% in one year, without adding any resources. In addition, employees enjoyed receiving bonuses as much as 50% of their annual income.
Work Experience:
• Lean-TPS Consultant / Coach 2015- Present
• Tekni-Plex LLC Continuous Improvement Engineer 2014 – 2015
Trained, Practiced and Repeated 5S technology company-wide, the foundation of Total Quality Management (TQM) to change company culture.
Initiated Problem Solving Team activity resulted in over 50% productivity improvement.
Introduced Poka-Yoke technology and 90% scrap reduction was achieved within four months.
Management team training, Linking hourly production issues with problem-solving teams, SMED, and Warehouse Optimization was introduced in related Tekni-Plex companies.
• Zodiac Seats US LLC Operations Excellence Leader 2012-2013
As an Operations Excellence Leader in a very demanding production environment led to quality training for production personnel, established Check &Repair stations at the end of each production process, and improved existing quality assurance work instructions. The result was 66% quality improvement in less than three months.
• Partner with Gemba Technology Research (GTR) Institute TOKYO-JAPAN 2001-2012
Shop Floor Management, hands-on-training for various industries including Automotive Manufacturing, Part Suppliers, Ship Building and Repair, Oil Refineries, Chemicals, Food, Textile, Tile Manufacturing, Health Care facilities, and Medical Centers.
Established Kaizen Website for information sharing on best practices and benchmarking.
Organized National Awards for Zero Defect Production Processes, and Best 5S Teams.
Worked closely with company management teams to develop strategies, trained employees as to how to adopt new Continuous Improvement Wave.
Established Lean Support System and trained the trainers to make a sustainable system.
Coordinated Japan Study Tours with my Japanese business partner to discover the reasons behind world-class Japanese companies’ successes. Valuable lessons learned from more than 40 world-class companies such as TOYOTA, NISSAN, YAMAHA, ROLAND YATAI, YAZAKI, and KONICA OPTICS.
• SAPCO Lean Manufacturing Department Head 1994-2001
Provided Lean Manufacturing training for any of the 500 part suppliers to improve business relationship with Supplying Automotive Parts Company (SAPCO). Trained Kaizen Promotion Officers to keep up with continuous improvements in a sustainable manner.
Established Lean Department at SAPCO to facilitate suppliers with knowledge and skills needed to create a more reliable and agile stream of components. More than 50 suppliers made quality and productivity improvements by 10% annually and made a secure business relation with the core company.
Created Employee Reward System at SAPCO to initiate continuous improvement driver for all company employees. The result was a 13% improvement in business metrics for just one year.
• Mobidic Glass Company Plant Manager 1993-1994
Improved Safety in processes, Production Planning, Sales and Marketing and reduced Scrap Rate by 20% within 5 months.
• Active Service as Naval Officer for 30 years.
Education and Training:
• BS. Naval Science- Britannia Royal Naval College, Dartmouth, England 1969
• Executive MBA. Industrial Management Institute, Tehran, Iran 1991
• Hands-on-training on Kaizen Concepts and Kaizen Technologies for 8 years, by Gemba Technology Research Institute, Tokyo, Japan President, Shuichi Yoshida, Founder of “NISSAN USA Quality Management System” as the first Japanese Auto Manufacturer operating in the USA. Nashville, TN 1983.
Technical Publications/ Memberships:
• Author of several technical papers with lean manufacturing topics to address the issues experienced through the processes of implementation.
• Research on Job Creation to improve employment.
• Member of Association of Iran-Japan Alumni (AIJA).
• Guest Speaker in several National Conventions and Seminars on Kaizen Concept and Technologies, Quality Improvement, Cost Management, Labor Productivity, and Total Productive Maintenance.
• Translated and published several Lean Manufacturing books, such as;
“Taichi Ohno’s Work Place Management”, Father of Toyota Production System. Prepared by the Japan Union for Scientists and Engineers (JUSE).
“Total Productive Maintenance,” written by Seiichi Nakajima. Father of TPM for Japan industries.
“Gemba Kaizen”, written by Masaki Imaie, Founder of Kaizen Institute of Japan.
Recognitions/ Certificate:
• National Best Practice Award won by one of my Quality Circle Trainees. 2009
• Several Appreciation Letters from company senior managers and organization heads.
• Certified DIN ISO 10011 QM- Lead Auditor QMA-TUV Academy. GmbH, Germany