Our story
Japan Study Tour
Professor Shuichi Yoshida, Gemba Technology Research President, Tokyo Japan, coached many companies in the USA, Europe, Fareast and the Middle East to improve productivity, profitability, and quality for more than two decades. TPS/Kaizen concept and technologies in a 5day Kaizen event was the kick off he executed as the wake-up call.
After a series of implementing on-site workshops at any one company, he provided another opportunity for his students to learn more from those who had been through many failures and successes to implement Kaizen at their own companies.
He organized Study Tours from successful industrial and service companies in different areas of Kaizen technologies, such as TPM, Low Cost Automation, S.M.E.D, QC Circles, Just In Time Production, VE/VA, Multi Skills Workers, R&D New Product Development, PPM, Customer Satisfaction, Cost Reduction, SCM, HRM and more.
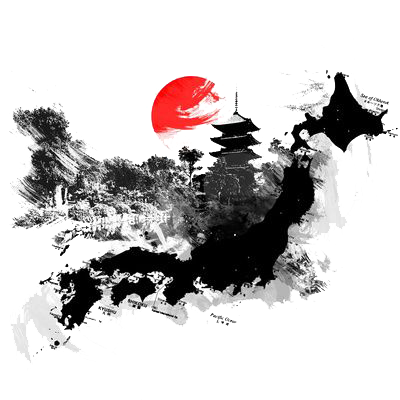
Managers, engineers, and supervisors who had enough experience in Kaizen and were eager to learn more from their Japanese counterparts had the chance to discover new facts from the Kaizen homeland, Japan and visit various companies and organizations, go to their Gemba, ask questions and discuss their issues with Japanese host company managers.
Ten companies in five days were visited in each JST, starting from Tokyo to Nagoya, the Toyota City. All JST members had to start early in the morning the first day. Get on the bus and go to the Tokyo Fish Market, be there before 06:00 am, and discover how this market being managed between 0600 to 0700am. After having breakfast the first day begins. Two places were visited each day. At the end of each day, stay in the pre-booked hotel for the night. All participants were advised to study the reading materials, provided in a special file about the next day host companies. All Study Tour Participants had to wake up early in the morning, do their own packing, have breakfast, check out from the hotel and get on the bus before 07:30 am. On the way to the host companies, Yoshida-san explained more about the company emphases and answered any question. This program repeated itself for 5 days.
On the way back from Nagoya to Tokyo, participants were expected to spend the 5 hours time on the bus, on group meeting and wrap-up what they had learned from each of the host companies, then make their report in writing and deliver a copy to Yoshida-san before leaving the bus.
The next day, JST members go to Narita Airport to fly back home having valuable souvenirs, lots of lessons learned.
JST Case Study: TOKYO FISH MARKET
Tokyo Metropolitan Government Central Wholesale Market
It is said that “ Uogashi” or a riverside fish market dates back to the 16th Century, the beginning of the Edo period. Tokugawa Ieyasu, the first Tokugawa shogun and Builder of Edo as is now Tokyo, invited fishermen from Tokudaijima, Osaka and gave them privilege for fishing in order to let them supply seafood to Edo Castle. The fishermen purveyed fish to the Castle and sold the remains near the Nihonbashi bridge.
Kaizen Company A
Emphasis: Digital Factory, Computer Aided Production System, Best Quality, Yatai System
Background of the Selection of the Host Company:
Kaizen Company established in the early 1980s as a manufacturer of music peripherals, is now making color inkjet printers and 3D laser canners. The products are assembled by the most advanced cell production system, which is aided by a computer.This unique and effective system designed by internal engineers.
Kaizen Company B
Emphasis: Low-Cost Automation (LCA), PPM, Single Minute Exchange of Dies (SMED), Efficient Production, 5S
Background of the selection of the host company:
The small and medium-sized companies are defined as companies having less than 500 employees and are financially protected by the Japanese government in many ways.They are classified into 3 kinds: The first type is an independent company that is marketing the specific products and technologies to an open market customer. The second type is a company that supplies the products to specific customers through its specific relationship with the customer. This relationship is called “ Keiretsu” or vertical integration of subcontracted companies. Keiretsu has many advantages as well as negative points.
Kaizen Company C
Emphasis: Deming Prize, TQM, U Shape Line Production,
Training, Part-Per-Million (PPM)
Background of the Selection of the Host Company:
In Japan, many good companies take up one of the three Kaizen programs (TQM, TPM, and JIT) at one time of the long history of the company to make their companies excellent companies. Though these three programs have overlapping areas, each has its special emphasis on actual implementation activities.
Kaizen Company D
Emphasis: High Tech-High-Precision Products, QC Circles, HRM.
Background of the Selection of the Host Company:
Any company tends to be inefficient and bureaucratic as it grows bigger and bigger. The result is to lose competitive power and to lose the entire business.As one of the business re-structuring measures to prevent this from happening as well as to start new business ventures, the so-called “Company System” is introduced (the first was established by Sony in 1994) at many companies in Japan in recent years. This system is more advanced than the IBU (Independent Business Unit) as this pseudo-independent company keeps its balance sheet and profit & loss statement under the corporate company.This company is one of these companies established when entirely new products were developed for the new market.
Kaizen Company E
Emphasis: TPM, LCA, Supply-Chain Management
Background of Selection of the Host Company:
Host Company is specialized in the design and production of small automotive, forklift and marine and industrial engines.To keep the company competitive, aggressive production improvement programs are being implemented including layout change. This company is utilizing old machines for efficient manufacturing production lines by use of TPM and LCA’s.
Kaizen Company F
Emphasis: JIT Production, TPS
Backgrounds of selection of the company:
Toyota Production System is called by various names such as Just-In-Time Production System, Kanban System (strictly speaking, this is some misleading), Lean Production System and Pull System. TPS is now extensively applied by non-automotive industry in Japan as well as abroad..
Kaizen Company G
Emphasis on QCCs, JST and Employee Suggestion Scheme, JIT Production System, In-House Training, TPM
Background of the selection of the host company:
This company is a huge enterprise in the making of automotive wire harnesses in Japan and overseas. (USA, Europe, South America, China & Asia)
The company has also diversified its products and operations and is keeping abreast of high efficient manufacturing capability, high-quality standards and new product development ability. In order to keep competitive, they are using Kaizen concepts and tools including QC Circles, JST and Employee Suggestion Scheme.
Nagoya, Toyota City, Home land of Toyota
Background of the selection of the host company:
Toyota Motors Corporation is the 4th larger automotive company (2004) in the world with many overseas plats. Toyota is a bench marking company with lean production system and TQM implementation as the guiding management principles. Toyota Kaikan, an annex to Toyota Motor, displays various aspects at automobile production processes from product design through final assembly operations plus environmental issues and new technologies. According to the latest information Toyota is now the biggest manufacturing company and the second largest automotive company next to GM in the world in 2004.